(4/25/2022)
Ensuring healthcare facilities secure necessary tools is a complex process. Additional challenges compounded quickly at the onset of the COVID-19 pandemic, which have since shifted the way organizations approach healthcare supply chain strategies. From identifying offshore versus onshore manufacturers and engaging in dual-sourcing to closely observing political changes and practicing foresight, healthcare facilities are able to set in motion new strategies that ensure their employees have the equipment they need.
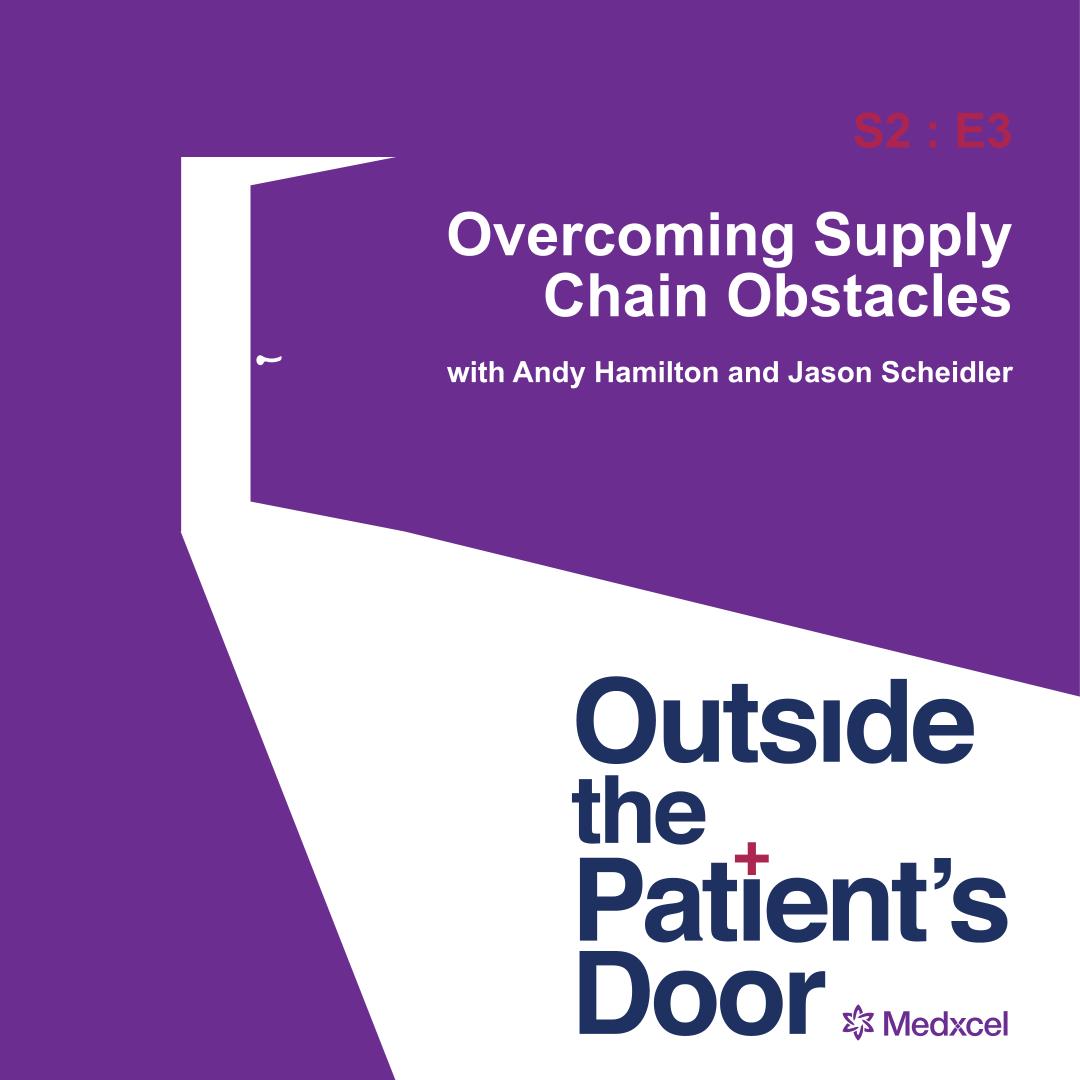.jpg?width=300&height=300)
Supply chain disruptions were first made apparent in January 2020 when China halted production at its factories due to the initial rapid spread of COVID. This most notably affected healthcare supplies like PPE, as China dominates the manufacturing of medical supplies globally. As COVID began its global spread and hospitals began experiencing a rush in emergency medical care, we saw how quickly current stocks were being depleted. Hospitals were no longer equipped to survive the rapid spread or increase in COVID cases.
This laid bare the gaps in strategies focused on the globalization of the supply chain, which formerly offered benefits such as lower costs, and added a new complexity to how markets around the world adjust in times of crisis.
Most notable supply chain challenges.
The emphasis on globalization of the supply chain quickly became apparent as the pool of potential vendors onshore was limited. The reliability of vendors also came into question as we were forced to start from scratch in an effort to source critical supplies at a rapid pace. When trying to fast-track a process like this, you really begin to test the limits of how quickly you can get products on site and the quality of that product. There were a lot of counterfeit products flooding the market, as well as products going undelivered. In addition, vendors were pushing the boundaries with more stringent contracts, requiring upfront payments and more because of the increased demand. Other challenges presented themselves for products that were not specific to healthcare but necessary to safety and operations, such as hand sanitizer and disinfectant wipes. Consumers and companies across all industries and around the globe were using these products exponentially more, limiting their availability.
Mechanisms to mitigate challenges, get ahead.
Businesses that weren’t previously deemed essential found ways to become essential in an effort to lend support and continue to serve their communities and employees. A great example of this included local distilleries producing hand sanitizers for hospitals and businesses or furniture manufacturers with appropriate tools that allowed them to produce critical PPE equipment. Dual-channel sourcing also came into play. Once regular channels began opening back up, there were more options and different approaches than what was once the traditional path.
Where we stand today.
While we are experiencing a shift back toward normal expectations, longer lead times continue to plague the supply chain, particularly for items coming from overseas. Shipping delays and backups or shutdowns at onshore and offshore ports can complicate timelines. Reliability and predictability are a concern, and backorders and recalls are increasing. Inflation adds a new layer of complexity, and is expected to have a huge impact on the supply chain moving forward – from fuel and freight expenses to recruiting and labor shortages.
Lessons learned.
The importance of balancing local and regional response with sourcing from a national command center can’t be overstated. Having a central command and support function focused on sourcing supplies and other items allowed local teams to focus on the issues more specific to their communities at any given time. Placing emphasis on evaluating and updating strategic plans to include risk and resiliency programs within the supply chain team can help prepare for future crises and challenges. Implementing supplier relationship programs that assess the performance of critical suppliers can also support supply chains success in both the short- and long-term.
To hear about the effects of supply chain disruptions and how to mitigate the challenges, check out Season 2, Episode 3 of our podcast,
Outside the Patient’s Door: “
Overcoming Supply Chain Obstacles with Andy Hamilton and Jason Scheidler.”