(9/19/2024)
As exciting as it is to see walls going up and buildings popping out of the ground, the preconstruction phase is where you can make the kinds of changes that can transform user experiences and avoid wasteful spend in meaningful and sustainable ways.
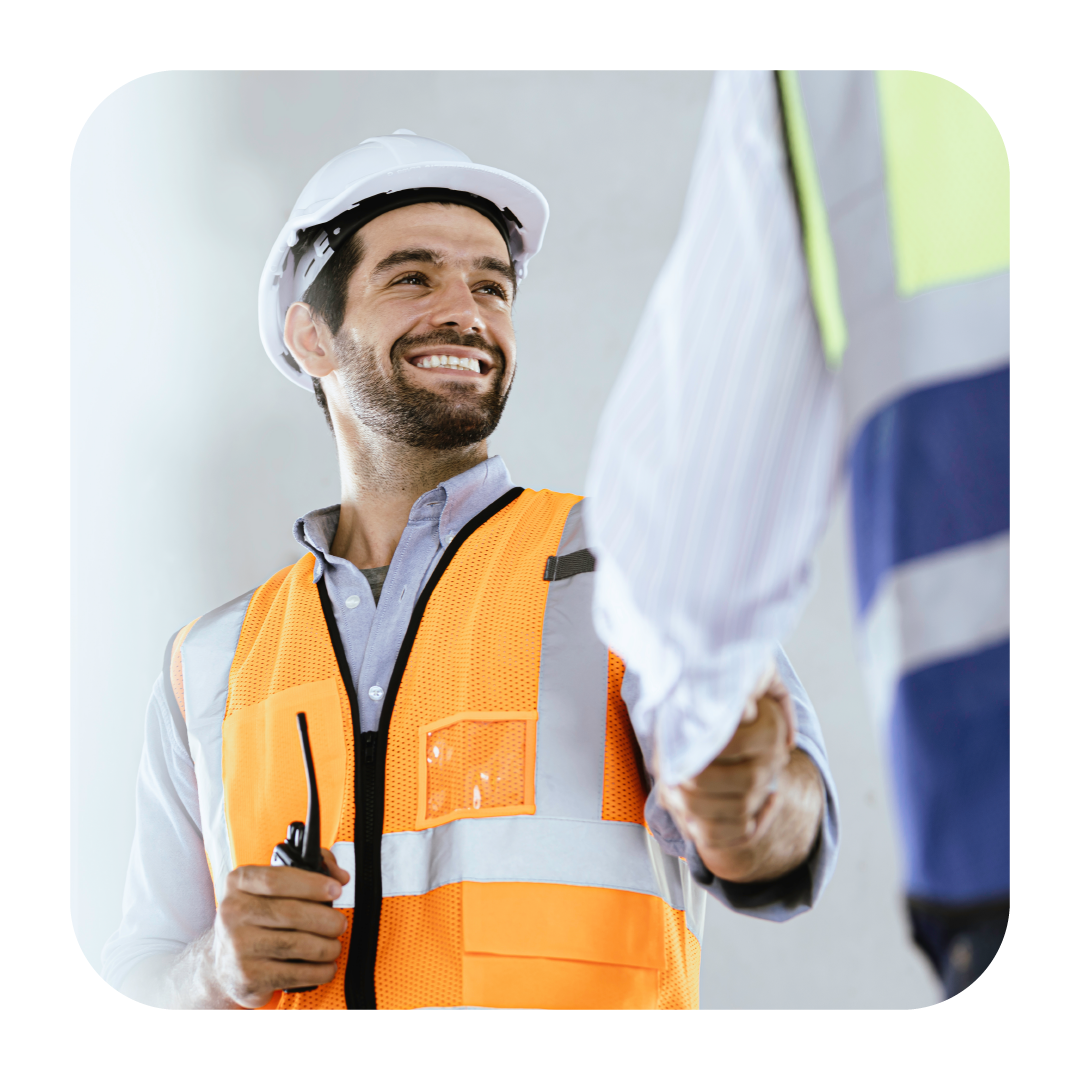
Among the myriad factors that go into quality patient care, one is, quite literally, a cornerstone of healthcare delivery: the physical environment. Patient safety, infection control, stress reduction, operational costs, staff morale and efficiency are just a small sampling of the ways building structures impact healthcare.
With so much at stake, healthcare leaders are wise to approach construction projects with an eye on both immediate and long-term implications to patient outcomes, operations, and cost efficiencies. As exciting as it is to see walls going up and buildings popping out of the ground, the preconstruction phase is where you can make the kinds of changes that can transform user experiences and avoid wasteful spend in meaningful and sustainable ways.
How the built environment helps or hinders healing
More than erecting attractive and comfortable structures, healthcare construction is awash in unique challenges ranging from complex regulations that vary from one region to another, to a slew of safety vulnerabilities, unlike any other industry. Nailing the right design, materials, suppliers, and approach for a healthcare construction project demands masterful planning by professionals who know construction and healthcare facilities management like the back of their hands.
Critical considerations in preconstruction planning include the following:
- Patient-centeredness, including…
- variable-acuity and single-bed rooms
- sufficient space to accommodate family members
- clearly marked signs to navigate the facility
- display monitors to easily access healthcare information
- Safety, including…
- improved availability of assistive devices to avert patient falls
- ventilation and filtration systems to control and prevent infections
- surfaces that can be easily decontaminated
- facilitated hand washing
- patient and provider injury prevention
- addressing the sensitivities associated with the interdependencies of care, including workspaces and processes
- Effectiveness, including…
- lighting for adequate visual performance
- use of natural lighting
- noise control
- Efficiency, including…
- standardized room layout, location of supplies and medical equipment
- minimal patient transfers to reduce safety threats and improve patient satisfaction
- Timeliness, including…
- rapid response to patient needs
- eliminating inefficiencies in the process of care delivery
- Equity, including…
- ensuring the size, layout, and functions of the structure meet the diverse care needs of patients
It’s a tall order, especially for builders who dabble, but don’t specialize in, the healthcare industry. It’s why hundreds of healthcare facilities across the U.S. lean on Medxcel for preconstruction expertise that will pay dividends for years to come, says Todd Paider, National Director, Construction Programs for Medxcel. “Every engineer, every project manager, every maintenance technician we have is fully dedicated to healthcare. That’s their life,” Paider shares.
Utilizing industry knowledge and partnerships to build for the future
Reasonably, you can’t unlock significant savings, nor big improvements in staff or patient experiences without deep mastery of the intricacies of healthcare environments. It’s even better when that mastery is backed by performance and predictive data which has benefited more than 2,600 healthcare facilities. Armed with those insights, Medxcel Planning, Design, and Construction (PDC) professionals can anticipate facility needs, potential problems, or opportunities with a high degree of accuracy and foresight. Our professionals follow a set of construction design and materials standards to maximize the value of each construction project while minimizing costs or risks for years to come.
“Our engineers foresee mechanical, electrical, or plumbing issues based on what we’ve seen in other client healthcare facilities. For instance, we know when extra space in an exam room becomes wasted space that would cost you more to build, maintain, and refurbish in the future,” Paider explains.
Medxcel PDC also brings that standardized approach to vendor contracts, securing below-market rates and better terms for client facilities. “We can pre-negotiate elements that aren’t industry standard, at lower costs. We often get extremely long warranties,” says Paider.
Elevating facilities with integrated facilities management
No single team or function can sustain high-performing facilities in isolation. Preconstruction planning is one of many puzzle pieces, interlocking and complementing one another to keep a healthcare facility safe, comfortable, and profitable. From landscaping to capital planning, ensuring patient focus and more, an effective facilities management program is one that pulls together all of those puzzle pieces shaping your facilities, all while maintaining regulatory compliance.
Because Medxcel also manages the facilities we build, there’s a great deal of collaboration between facilities functions at every stage, from preconstruction to postconstruction and day-to-day facilities management. As many facilities leaders have found, working with a complete puzzle can be a massive advantage, freeing up significant time, effort, and dollars.
Learn more about how Medxcel's PDC solution can elevate your facilities management: medxcel.com